CAD – ERP Integration
Not just for Engineering Data Handoff
Synchronizing CAD/PDM/PLM data like SOLIDWORKS, Autodesk products, or PTC Windchill with ERP systems like NetSuite, SAP, IFS, Business Central, or Oracle JD Edwards can indeed vary based on roles or process steps, depending on the nature of the workflow and the specific needs of the organization. Here’s a breakdown:
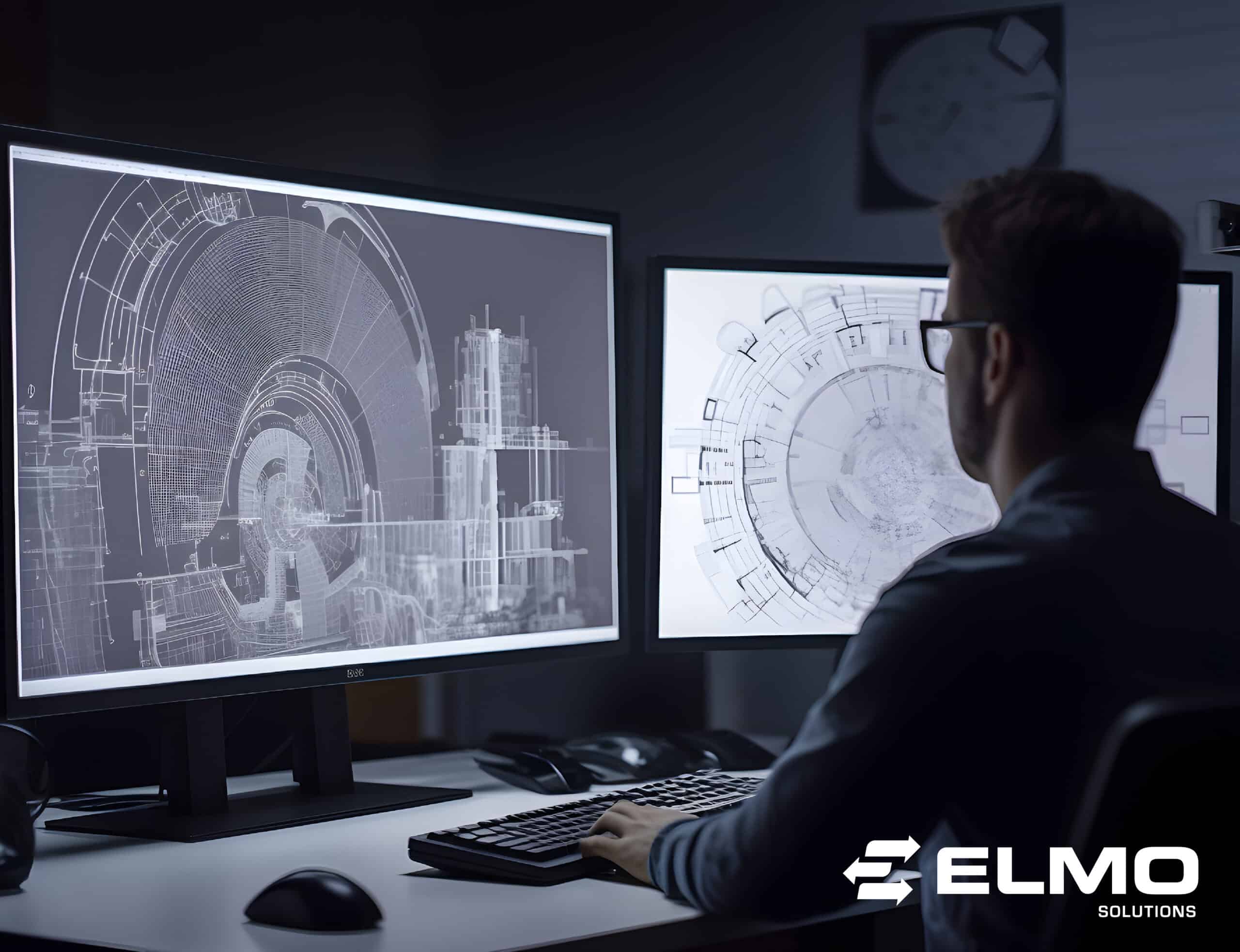
By Role:
– When to synchronize: During product releases, especially when transitioning from engineering to manufacturing.
– Why: Product managers oversee the broader lifecycle of a product and are responsible for ensuring that product data, including new revisions or updates, is properly communicated to downstream systems like ERP. This typically happens when the design is finalized and ready for production, meaning CAD data needs to be synchronized to reflect the final design or any revisions made.
2. Product Editors/Designers:
– When to synchronize: At each “check-in” of design updates.
– Why: Designers may need to frequently update CAD data, and synchronizing with the ERP ensures that all stakeholders have access to the latest versions of parts, assemblies, and other design components. Frequent synchronization at the check-in stage can prevent discrepancies and keep the development process smooth.
3. Project Managers:
– When to synchronize: After completing the entire layout of a project.
– Why: Project managers may oversee larger aspects of the project, such as coordinating various teams and managing the project timeline. Synchronization at this stage ensures that the finalized layout and its associated BOMs (bill of materials) and assemblies are accurately captured in the ERP system for procurement, production, and logistics.
By Process Step:
– When to synchronize:Â When the item reaches a certain status in the workflow, like design approval or pre-production.
– Why: Synchronizing at this status ensures that the latest data is captured and that ERP systems are updated before moving to the next critical step in the process, such as manufacturing.
2. Check-In
– When to synchronize: Upon checking in design updates or changes in a PDM/PLM application.
– Why: This captures incremental design changes and keeps all systems aligned, reducing the risk of design discrepancies or errors during the development process.
3. Sub-Assemblies
– When to synchronize: As sub-assemblies are created or modified.
– Why: Synchronizing sub-assemblies ensures that all components are correctly tracked and available in the ERP for use in higher-level assemblies, procurement, or production planning. It is possible to merge a sub assembly created in an Electrical CAD to a Mechanical CAD Systems.
Agni Link from Elmo Solutions
Agni Link from Elmo Solutions is designed to adapt to both role-based and process step-based synchronization needs. For example:
- Role-based needs: Agni Link can allow different users (like product managers or designers) to trigger synchronization based on their specific tasks and responsibilities. The behaviours for each field can be different depending on user’s role.
- Process-based needs: The tool can trigger synchronization at key workflow points, such as when a design reaches a specific status or when a sub-assembly is ready.
In summary, the timing of synchronization depends on the context and business processes within a company—whether it’s driven by the role of the user or the specific process step in the workflow. By utilizing a flexible solution like Agni Link, companies can tailor their synchronization approach to their unique needs.

Matthew Bui is the Partner Success Manager at Elmo Solutions, a world class leader in CAD/PDM/PLM – ERP data integration. He is a quality-oriented business executive with a proven track record in international business, global partnerships and customer service. To contact Matthew email .
Elmo Solutions Inc.
797, boul. Lebourgneuf, suite 300
Quebec (Quebec) G2J 0B5