Digital Transformation in Engineer-to-Order(ETO) Companies: Where to Begin?
Globally, some of the most digitally transformed ETO companies can be found in Germany, the United States, and Japan. These countries are at the forefront of integrating digital tools into manufacturing and engineering processes, leveraging Industry 4.0 innovations, AI-driven automation, and smart factory initiatives.
In an increasingly digital world, Engineer-to-Order (ETO) companies—such as those in Industrial Machinery Manufacturing, Automation Machinery Manufacturing, Packaging & Containers Manufacturing, and Paper & Forest Products Manufacturing—face unique challenges. Unlike standard manufacturing, ETO businesses create highly customized products, often dealing with complex supply chains, shifting customer requirements, and extensive engineering cycles. Digital transformation offers ETO companies a path to greater efficiency, agility, and profitability—but where should they begin?
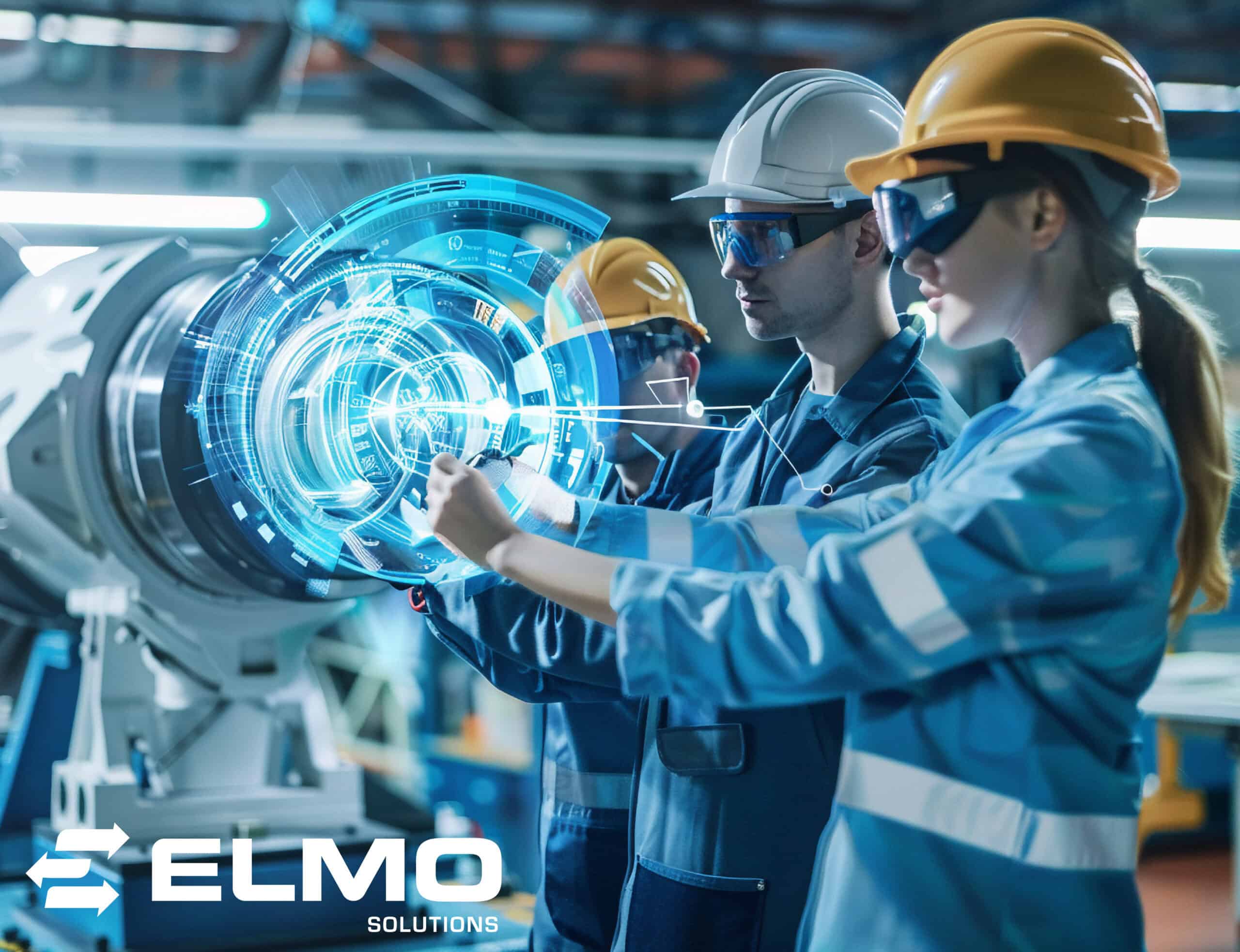
What Digital Transformation Means for ETO Companies
Digital transformation in ETO companies is not just about adopting new technologies; it’s about fundamentally rethinking processes to improve efficiency, collaboration, and customer satisfaction. It involves leveraging digital tools to streamline engineering, automate workflows, and enhance decision-making.
Some key areas where digital transformation impacts ETO businesses include:
- Integrated Engineering and Manufacturing Systems – Implementing Product Lifecycle Management (PLM) and Enterprise Resource Planning (ERP) systems (such as Solidworks, Autodesk, AutoCAD, TeamCenter, Windchill for PLM, and NetSuite, Business Central, IFS, SAP, Priority, Acumatica, and Industrios for ERP) ensures seamless communication between design, engineering, and production teams.
- Automated Quoting and Configuration – Using AI-powered Configure, Price, Quote (CPQ) solutions enables faster and more accurate quoting, reducing the sales cycle time.
- Advanced Simulation and Virtual Prototyping – Digital twins and CAD-driven simulations help validate designs early, minimizing errors and costly physical prototyping.
- Real-Time Collaboration and Data Sharing – Cloud-based platforms and IoT connectivity allow teams to access real-time project data, improving coordination and reducing rework.
- Supply Chain Optimization – AI and analytics-driven supply chain management tools improve demand forecasting, supplier coordination, and material tracking.
Where Should ETO Companies Start?
Digital transformation is a journey, and ETO businesses should take a structured approach to avoid overwhelming complexity. Here’s how to get started:
- Assess Current Processes and Pain Points
Before implementing new technologies, companies should conduct a thorough audit of their current processes. Identifying bottlenecks in design, procurement, or production will help prioritize digital initiatives with the highest ROI.
- Develop a Clear Digital Strategy
Leadership must align digital initiatives with business goals. Whether improving lead times, reducing costs, or enhancing customer experience, having a clear vision ensures investments yield tangible benefits.
- Invest in Scalable Technologies
Companies should begin with foundational technologies such as ERP, PLM, and CPQ, ensuring seamless data flow between departments. Cloud-based solutions provide flexibility and scalability for future expansions.
- Foster a Digital Culture
Digital transformation is not just about tools—it’s about people. Training employees, encouraging collaboration, and promoting a culture of innovation will drive successful adoption.
- Start Small and Scale Gradually
Rather than attempting a company-wide overhaul, businesses should pilot digital initiatives in one department or process. This approach minimizes risk while demonstrating quick wins, building momentum for broader transformation.
The Road Ahead
For ETO companies, digital transformation is not a one-time project but an ongoing evolution. By embracing digital tools and rethinking traditional workflows, these businesses can enhance agility, improve profitability, and deliver superior customer experiences.
The key is to start with a clear strategy, focus on high-impact areas, and ensure teams are equipped for the digital future. The journey may be complex, but the rewards are well worth the effort.
A crucial tool for this journey is Agni Link from Elmo Solutions, which helps ETO companies bridge the gap between engineering and manufacturing data. By seamlessly integrating CAD, PLM, and ERP systems, Agni Link ensures accurate, real-time data synchronization, reducing errors and improving efficiency across departments. This integration enables smoother workflows, faster production cycles, and greater overall productivity—key components of a successful digital transformation strategy.
Are you ready to begin your digital transformation journey? Start by identifying your most pressing challenges and exploring the technologies that will drive meaningful change for your business.

About the Author
Matthew Bui is the Partner Success Manager at Elmo Solutions, a world class leader in CAD/PDM/PLM – ERP data integration. He is a quality-oriented business executive with a proven track record in international business, global partnerships and customer service. To contact Matthew email .
Elmo Solutions Inc.
797, boul. Lebourgneuf, suite 300
Quebec (Quebec) G2J 0B5