The Challenges of BoM Management in a ETO Manufacturing
What strategies do Engineered to Order manufacturers use when synchronizing assemblies and
subassemblies data from their CAD/PDM/PLM systems to their ERP?
By Matthew Bui
When synchronizing data from a CAD (Computer-Aided Design), PDM (Product Data Management), or PLM (Product Lifecycle Management) system to an ERP (Enterprise Resource Planning) system, “levels” typically refer to the hierarchical structure of the product data. This hierarchical structure is crucial for organizing and managing complex products and their associated data. A Bill of Materials is usually modeled as a tree. The root is at level zero. Below the root, each node is one level deeper: level 1 for the children, level 2 for the grandchildren, level 3 for the great-grandchildren, … A level is defined by the relationship between a parent assembly and its components. The components can be parts or subassemblies. Embedding an assembly into another assembly creates a multi-level BOM.
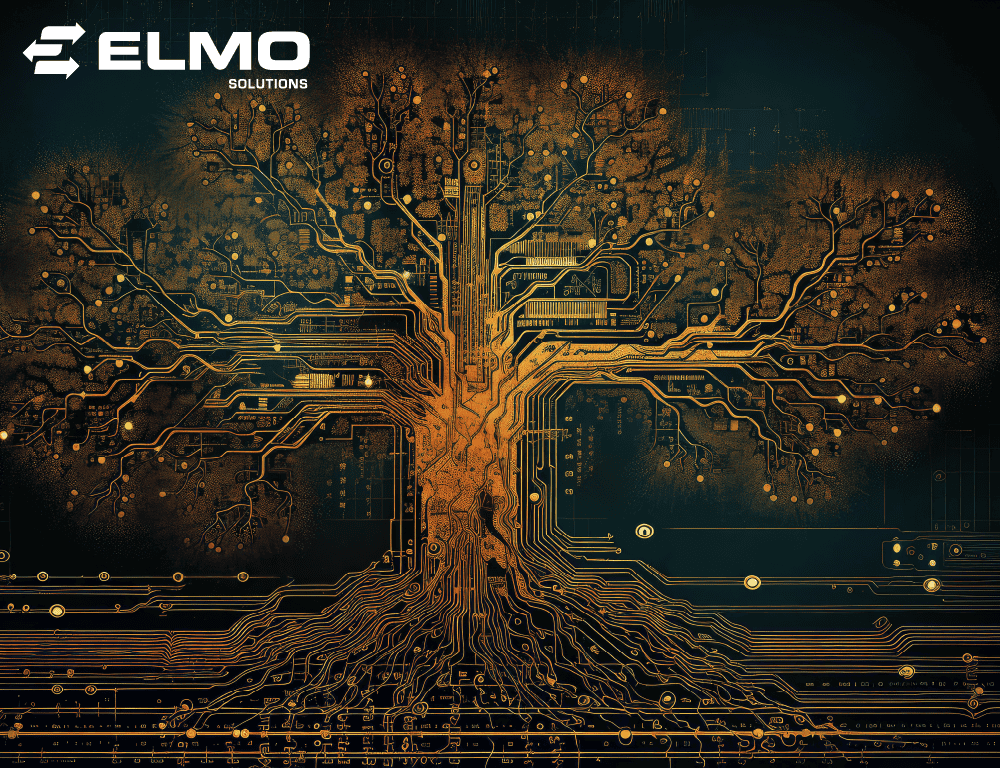
Here’s what the levels generally represent:
1. Product Structure/Bill of Materials (BOM):
-
-
- Top-Level (Level 0): This is the highest level in the hierarchy, usually representing the finished product or the final assembly.
- Subassemblies (Level 1, 2, etc.): These are the components or subassemblies that make up the top-level product. Each subassembly can have its own components, creating additional levels in the hierarchy.
- Individual Parts (Lowest Levels): These are the individual components that make up the subassemblies and ultimately the final product. They are the most granular level in the BOM.
-
2. Data Hierarchy: Data is associated with that relationship in the context of a BOM: a quantity (an integer number, how many times that part is used to build that assembly) and a unit of measurement (unit, piece, each, …).
-
-
- Product Data: Information related to the overall product, such as drawings, design specifications, performance criteria, and regulatory compliance data.
- Assembly Data: Information about the assemblies, including assembly instructions, fit and tolerance data, and interaction with other assemblies.
- Part Data: Detailed data on individual parts, such as material specifications, manufacturing processes, and supplier information.
-
3. Attributes and Metadata:
-
-
- Global Attributes: Information applicable to the entire product or assembly, such as part numbers, descriptions, and lifecycle states.
- Local Attributes: Specific details related to individual components, like dimensions, weight, and material type.
-
In essence, these levels help ensure that all necessary information about the product structure and its components is accurately transferred and mapped in the ERP system. This hierarchical data is crucial for various business processes, such as manufacturing, procurement, inventory management, and order fulfillment. By carefully managing these levels and ensuring accurate synchronization, organizations can improve the efficiency of their product development, manufacturing, and resource planning processes.
What are the complexities ETO machinery manufacturers face regarding the synchronization of complex multi-level BOMS from their CAD/PDM/PLM systems?
Engineered to Order (ETO) machinery manufacturers face several complexities when synchronizing multi-level Bills of Materials (BOMs) from their CAD/PDM/PLM systems to their ERP systems. They can have multiple parts and assemblies to synchronize between their ERP systems. If done manually, multiple pages would need to be opened, compared and uniformized. The problem gets more and more challenging, slow and error-prone with multi-level BOMs since multiple different pages on both systems need to be opened, compared and uniformized. Due to the nature of ETO businesses, this process needs to be done frequently raising challenges that can significantly impact their efficiency, accuracy, and overall productivity. Here are the primary challenges:
1. Complexity of Multi-Level BOMs:
-
- Detailed Structures: ETO products often involve highly detailed and custom BOMs with multiple levels of subassemblies and components, making it challenging to ensure all details are accurately captured and transferred.
- Customization: Each project may have unique requirements, leading to frequent changes and additions to the BOM, which need to be meticulously managed.
2. Data Consistency and Integrity:
-
- Inconsistencies: Discrepancies can occur between the BOMs in CAD/PDM/PLM systems and those in the ERP system, leading to errors in production and procurement.
- Data Accuracy: Ensuring that all parts, assemblies, and materials are accurately represented and synchronized across systems is critical to avoid costly mistakes.
3. Change Management:
-
- Frequent Updates: ETO projects often undergo numerous design changes. Synchronizing these changes in real-time between CAD/PDM/PLM and ERP systems is challenging but necessary to maintain up-to-date information.
- Revision Control: Managing different revisions of BOMs and ensuring the ERP system reflects the most current revision is crucial.
4. Integration Complexity:
-
- Different Data Formats: CAD/PDM/PLM and ERP systems often use different data formats and structures, requiring robust integration tools to translate and map data accurately.
- System Compatibility: Ensuring compatibility between different software systems and their versions can be technically challenging and resource-intensive.
5. Lifecycle and Workflow Synchronization:
-
- Lifecycle States: Aligning lifecycle states (e.g., design, prototype, production) between CAD/PDM/PLM and ERP systems to ensure consistent workflow and status tracking.
- Workflow Coordination: Synchronizing workflows between engineering and manufacturing departments to ensure smooth transitions and handoffs.
6. Data Volume and Granularity:
-
- Large Data Sets: Managing and transferring large volumes of detailed data, including specifications, drawings, and metadata, can be resource-intensive.
- Granularity: Ensuring that the detailed information at each BOM level is accurately captured and reflected in the ERP system.
7. Supply Chain Coordination:
-
- Procurement Challenges: Accurate BOM synchronization is critical for procurement planning and supplier coordination. Any errors can lead to delays and increased costs.
- Lead Times: Managing lead times for custom parts and materials, and ensuring the ERP system reflects accurate availability and scheduling information.
8. Human Factors:
-
- Manual Data Entry: Reliance on manual data entry increases the risk of errors and inconsistencies. Automating data synchronization is essential but can be complex to implement.
- Training and Expertise: Ensuring that staff are adequately trained to use integrated systems and understand the synchronization process.
9. Compliance and Documentation:
-
- Regulatory Compliance: Ensuring that all synchronized data meets regulatory standards and documentation requirements.
- Traceability: Maintaining traceability of all components and materials throughout the product lifecycle.
How Agni Link from Elmo Solutions is streamlining the synchronization of multi-level BOMs
Agni Link is the most advanced CAD-ERP integration system currently available. It is an add-in to your CAD/PDM/PLM that offers a unique, reliable and cost-effective way to synchronize multi-level BOMS with virtually any ERP system.
Agni Link can support and manage all different BOM structures that are created by CAD/PDM/PLM applications including the creation of multi-level indented BoM structures. Raw materials are also supported and would add an additional level to the structure. Agni Link can synchronize all the levels of a whole assembly in a single step.
From the end-user perspective, all the BOM levels are simultaneously displayed in the Agni Link Integration Dashboard and each level has its own line in the Dashboard.
All the data coming from both systems (CAD/PDM/PLM and ERP) are displayed simultaneously in the Integration Dashboard including the values read from the different pages in both systems. Each data point has its own column in the Dashboard.
The synchronization of all levels and nodes in the BOM tree can be validated in a single grid of the Dashboard. This can be completed automatically, once validated by the end-user, by clicking a single “Synchronize” button in the Integration Dashboard.
Agni Link can do these synchronizations repeatedly, consistently and rapidly providing incredible value and automation to Engineered to order manufacturers in industries where assemblies or sub-assemblies are reused in new project deliveries.

About the Author
Matthew Bui is the Partner Success Manager at Elmo Solutions, a world class leader in CAD/PDM/PLM – ERP data integration. He is a quality-oriented business executive with a proven track record in international business, global partnerships and customer service. To contact Matthew email .
Elmo Solutions Inc.
797, boul. Lebourgneuf, suite 300
Quebec (Quebec) G2J 0B5