Integrating Design and Manufacturing Data?
When is the best time to start?
Embarking on an ERP (Enterprise Resource Planning) implementation whether it’s Oracle NetSuite, SAP, Microsoft Dynamics 365, IFS, or Priority Software is a significant step for any business. One of the critical aspects to consider early in this process is the integration between your design and manufacturing data, especially when working with CAD systems like AutoCAD, SolidWorks, PTC Windchill, EPLAN, or Siemens Teamcenter.
Manufacturing companies in Engineered-To-Order (ETO), Built-To-Order (BTO), and Made-To-Order (MTO) environments should prioritize design-to-manufacturing data integration early in their ERP implementation for several compelling reasons.
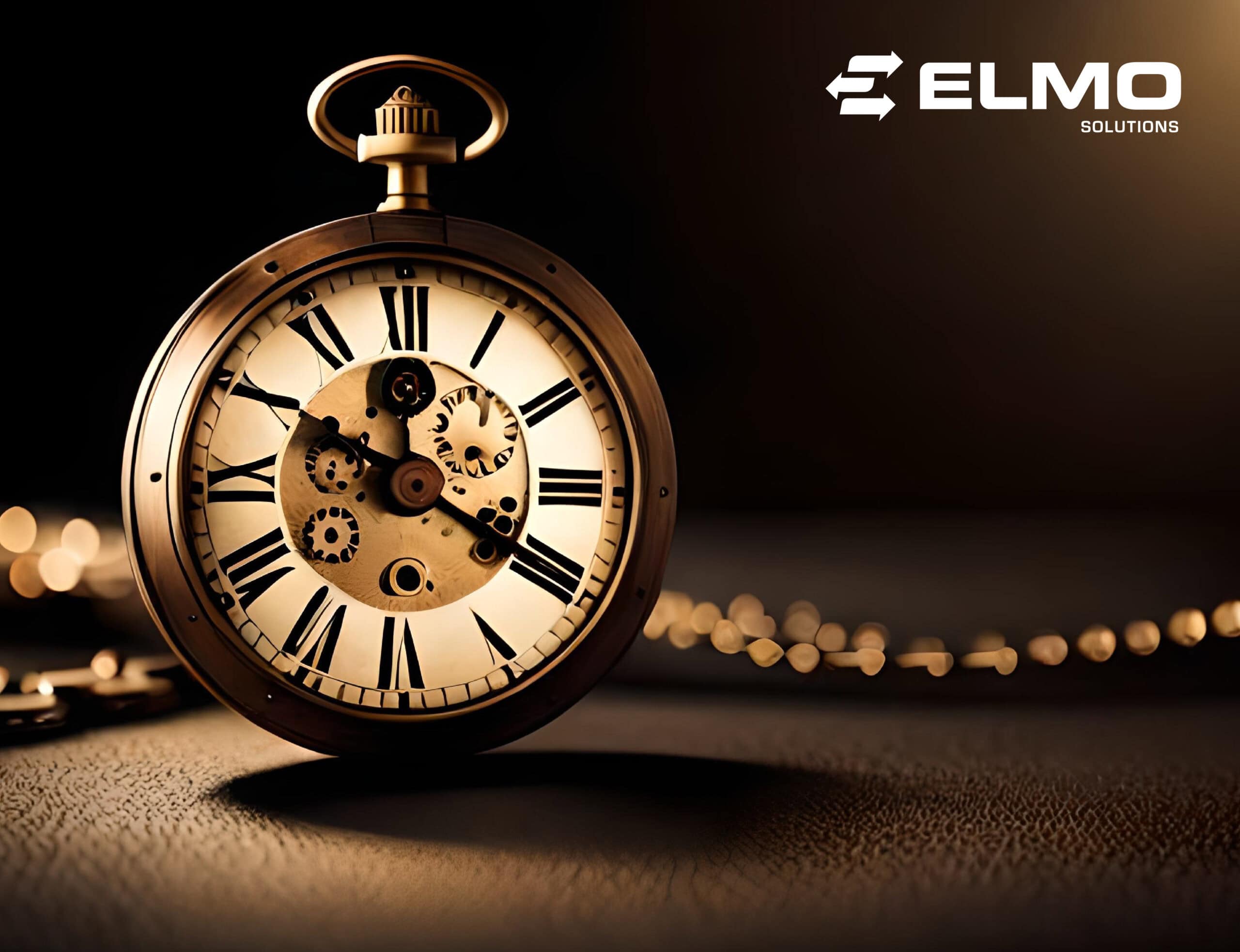
Complexity and Customization of Orders
- ETO, BTO, and MTO environments deal with highly customized products, requiring tight coordination between design, engineering, and production. Integrating CAD, PDM, PLM, and ERP systems early ensures that complex product designs flow seamlessly into manufacturing and procurement processes.
- Early integration reduces the risk of errors in transferring custom designs into production, minimizing delays or cost overruns caused by incorrect BOMs (Bill of Materials) or inaccurate specifications.
Efficient Product Lifecycle Management
- In these environments, each product may have a unique lifecycle. Design-to-manufacturing data integration ensures the seamless transfer of Bill of Materials (BOMs), part specifications, and engineering changes into ERP, which governs production and logistics.
- Without integration between systems like Siemens Teamcenter and Priority Software, design changes or product revisions can lead to miscommunication between departments, causing production delays, higher scrap rates, and incorrect procurement of materials.
Improved Collaboration Between Departments
- Design and engineering teams typically work with CAD/PDM/PLM systems like SolidWorks or AutoCAD, while manufacturing, procurement, and finance rely on ERP systems such as IFS or Oracle NetSuite. Early integration improves communication and collaboration between these departments by eliminating data silos.
- Integrated systems create a single source of truth where design data, costing information, and manufacturing instructions are available to all stakeholders in real time.
Streamlined Data Flow and Reduced Manual Processes
- ETO, BTO, and MTO manufacturing environments often involve repetitive manual entry of data from CAD systems into ERP systems. This is both time-consuming and prone to errors.
- By integrating design data from systems like Siemens SolidEdge or EPLAN with ERP systems like Microsoft Dynamics 365 or IFS early companies can automate these transfers, improving accuracy, speeding up the order fulfillment process, and freeing up resources for more value-added activities.
Faster Time-to-Market
- Early integration CAD systems like Autodesk Vault with ERP platforms such as Acumatica accelerates the order-to-production cycle, enabling companies to respond more quickly to customer demands and changes in product specifications.
- This is particularly important in ETO and BTO environments, where custom designs need to be manufactured on short notice. Automated data flows between CAD and ERP mean that production can begin sooner, reducing lead times.
Better Cost Control and Quoting Accuracy
- ERP systems like SAP or Oracle NetSuite often contain critical information about materials, inventory levels, labor costs, and supplier relationships. By integrating design data with the ERP system, companies can obtain more accurate costing information during the design phase.
- This is crucial in ETO/BMTO environments, where accurate quotes depend on precise costing and material availability. Early integration allows the engineering team to have visibility into cost impacts early on, leading to more competitive and realistic pricing for customers.
Enabling Engineering Change Management
- In ETO environments, engineering changes are frequent, and they can have significant downstream impacts on production, procurement, and delivery.
- Early integration between Solidworks and ERP platforms such as Microsoft Dynamics 365 facilitates engineering change management by automatically updating BOMs, part numbers, and specifications across all systems. This ensures that changes are captured in real-time, preventing miscommunication and production of outdated designs.
Risk Mitigation
- Delaying design-to-manufacturing data integration until after ERP go-live increases the risk of issues such as data mismatches, incorrect inventory levels, and production inefficiencies.
- Early integration provides more time to identify and resolve any potential technical or process-related issues before going live, reducing risks during the critical early stages of ERP implementation.
Foundation for Future Digital Transformation
- Integrating design data from systems like EPLAN or Autodesk Revit with ERP platforms like IFS or Priority Software early in the ERP journey lays the groundwork for future digital transformation initiatives such as Industry 4.0, IoT (Internet of Things), and digital twin
- With a strong integration between design and manufacturing, companies can move towards advanced manufacturing practices, predictive maintenance, and better supply chain visibility.
It’s essential to start planning this integration as soon as you have access to your ERP sandbox and begin configuring your ERP system. Here’s why:
Business Process Decisions Will Influence Integration Complexity
The decisions made about business processes during ERP implementation will directly affect how smoothly your design and manufacturing data can be integrated. Whether you’re aligning bills of materials (BOMs), managing change orders, or tracking production timelines, these processes are often tightly intertwined with both design and manufacturing data.
By planning the integration early, you can ensure that data flow and structure align with your specific business processes, making it easier to automate workflows and avoid rework down the line.
Reduce Data Silos and Enhance Collaboration
Design teams often use different tools (such as CAD systems) compared to manufacturing teams, which rely on production planning software. Without a well-planned integration, data silos can emerge, making collaboration difficult and increasing the chances of errors.
Early integration planning can bridge these gaps, enabling seamless data sharing between design and manufacturing departments. This allows teams to collaborate effectively and maintain consistency across product development, from the design phase through to production.
Ensure Compatibility with Existing Systems
Your ERP system needs to be compatible with the tools and systems already in use for managing design and manufacturing data. Starting the integration process early gives you the time to evaluate compatibility issues and configure Agni Link correctly. This ensures that data is transferred efficiently and accurately across systems, reducing bottlenecks and errors during production.
Simplify Future Scalability
ERP systems are designed to grow with your business. If you plan for integration from the outset, it’s easier to scale as your design and manufacturing processes evolve. The right decisions early in the ERP implementation will make it simpler to integrate new tools or technologies without disrupting current workflows.
To get started with the CAD to ERP integration using Agni Link, here’s a structured checklist based on the provided information:
Access to ERP Sandbox Environment
- ERP Sandbox: Ensure you have a test environment that mirrors your production ERP. This allows testing without affecting live data.
Test Computer Setup
- Sandbox for CAD/ERP Systems: The test computer must be connected to sandbox environments for both the CAD and ERP systems.
- Necessary Software: CAD (or ECAD), PDM, or PLM applications must be installed (AutoCAD Mechanical, Autodesk Inventor, Autodesk Vault, SolidWorks CAD, SolidWorks PDM, Siemens Teamcenter, PTC Windchill, etc…).
CAD/PDM/PLM Applications
- Agni Link Installation: Install Agni Link as an add-in to the selected CAD/PDM/PLM application on the test computer.
- Test Assets: Prepare a small, isolated assembly of 15 parts or less. These test assets should reflect your production files, including all relevant properties.
ERP Client
- ERP Configuration: The ERP client must be installed and configured on the test computer.
- User Account: A valid ERP user account (username and password) must be created and provided for validation of the CAD-ERP synchronization.
ERP Database
- Production-like Data: Ensure the ERP database or environment contains real or representative production data for testing and validation.
Development Environment
- Installed Development Tools: Make sure the necessary development environment is installed on the test computer.
- Permissions: Proper permissions should be granted to allow the Elmo Solutions team to customize the setup, including access to expose web services and modify objects.
Web Services Components
- Web Services Setup: Agni Link primarily communicates with ERP via web services. Ensure web services are set up correctly.
- Alternative Methods: If the ERP system does not support web services, ensure the appropriate SQL queries and API access are available for connectivity.
Conclusion
Early integration between CAD/PDM/PLM and ERP systems enables accurate data flow, reduces the risk of errors and delays, and ensures that complex, customized products can be manufactured efficiently in ETO, BTO, and MTO environments. Starting integration as soon as the ERP sandbox is available gives companies a competitive advantage by improving collaboration, cost control, and overall operational efficiency.

Matthew Bui is the Partner Success Manager at Elmo Solutions, a world class leader in CAD/PDM/PLM – ERP data integration. He is a quality-oriented business executive with a proven track record in international business, global partnerships and customer service. To contact Matthew email .
Elmo Solutions Inc.
797, boul. Lebourgneuf, suite 300
Quebec (Quebec) G2J 0B5